Factory Progression of Production (Working, Idle, & Problem) Timers All in 1 Enclosure
- By : DC-Digital sales & marketing
- Category : Count Up timer, Elapsed Timer, Manufacturing, Timers
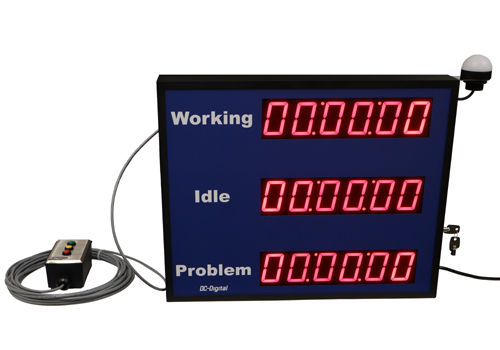
Optimizing Factory Efficiency with a Triple Timer System: A Game-Changer for Production
In today’s fast-paced manufacturing environment, managing time efficiently is essential for maximizing productivity, minimizing downtime, and ensuring that production processes run smoothly. To address these challenges, the introduction of a Triple Timer System—a smart and simple solution for tracking multiple phases of a factory production process—can be a game-changer. This system ensures that every minute is accounted for, helping businesses improve both operational efficiency and profitability.
What is the Triple Timer System?
The Triple Timer System is an innovative tool designed to keep track of three critical stages in the production process: working time, idle time, and problem time. These three timers are housed within a single enclosure, offering a compact and efficient solution for managing production workflows. With a simple interface, the system makes it easy to monitor and record these stages without the complexity of multiple devices.
Key Features of the Triple Timer System
- Three Timers in One Enclosure:
- Working Time: This timer tracks the active production process. Every second spent on manufacturing, assembling, or processing is recorded here. By keeping an accurate count of working hours, managers can assess productivity and determine whether the workforce is meeting production goals.
- Idle Time: This timer keeps track of periods when the production process is not actively running, such as during lunch breaks, shift changes, or machine downtime. Monitoring idle time helps identify opportunities for process improvement and reduce unnecessary delays.
- Problem Time: This timer tracks periods when the production process is halted due to issues like machine malfunctions, quality control failures, or material shortages. By isolating problem time, businesses can analyze root causes, implement solutions, and reduce recurring issues.
- Wired Remote Control:
- Each timer is controlled via a wired remote, making it easier for operators to manage the timers without needing to interact directly with the enclosure. With the push of a button, operators can start, stop, and switch between timers. This is especially helpful when workers are focused on production tasks and need a quick way to switch between stages of the process.
- Importantly, only one timer can be active at a time, preventing any confusion or overlap in tracking time. The remote allows operators to seamlessly transition from one timer to the next, ensuring that each stage is accurately recorded.
- Master Reset Key Switch:
- Once the production process is completed, it’s time to reset everything and prepare for the next cycle. The Master Reset Key Switch is a crucial feature that ensures all three timers—working, idle, and problem time—are reset to zero. This guarantees that data from previous cycles doesn’t interfere with future processes.
- Only authorized personnel can reset the system, adding an extra layer of control to ensure that all data is cleared properly before beginning the next production cycle.
- ANDON Light for Status Indication:
- One of the most intuitive features of the Triple Timer System is the ANDON light. This light provides a clear, visual indication of which timer is currently running, offering immediate feedback for both operators and supervisors.
- The ANDON light changes colors based on the active timer:
- Green: When the working time timer is active, the ANDON light will glow green, signaling that the production process is running smoothly and on track.
- Yellow: When the idle time timer is active, the ANDON light will turn yellow, indicating that production is paused for a non-productive reason, such as a break or a shift change.
- Red: When the problem time timer is running, the ANDON light will turn red, signaling that there’s a production issue that requires immediate attention. This visual cue helps operators and supervisors identify problems quickly and act to resolve them.
- The ANDON light ensures that everyone on the factory floor can easily understand the current status of the production process without needing to check the timers manually.
How the Triple Timer System Boosts Efficiency
- Precise Time Management: By accurately tracking working, idle, and problem time, manufacturers can gain insights into how time is spent during each production cycle. Managers can use this data to identify inefficiencies, streamline processes, and optimize workflows. For example, if idle time is consistently high, it may signal the need for better shift planning or faster equipment changeovers.
- Data-Driven Decision Making: The ability to track problem time helps manufacturers identify patterns in equipment breakdowns or production interruptions. With this data, maintenance teams can be more proactive in scheduling repairs or addressing recurring issues before they cause significant delays. This data can also be used to refine training programs or process designs to minimize problems in the future.
- Increased Accountability: The transparent tracking of time spent in each phase of the production process encourages accountability across the workforce. Workers are more likely to stay focused on tasks when they know that their time is being monitored. Furthermore, the system can highlight areas where additional training or support may be needed, helping workers improve efficiency and reducing errors.
- Better Resource Allocation: By understanding the distribution of time between work, idle periods, and problems, companies can better allocate resources. If problem time is high, it may be necessary to invest in more reliable equipment or enhance troubleshooting procedures. Similarly, if idle time is significant, efforts can be made to reduce unproductive periods, such as adjusting break schedules or improving material supply chains.
- Simplicity and Convenience: One of the main selling points of the Triple Timer System is its simplicity. Operators can quickly adjust timers through the wired remote, and the system is easy to set up and use. Unlike complex time-tracking software or manual logbooks, the Triple Timer System allows for immediate, accurate tracking without any unnecessary hassle.
- Instant Visual Feedback with ANDON Light: The ANDON light offers a simple yet powerful visual indication of the current timer status, giving workers and managers immediate insight into what stage of production is active. This instant feedback improves communication, enables quicker problem identification, and helps keep the factory floor running smoothly.
A Seamless Integration into Your Production Line
Whether you’re operating a small factory or a large-scale production line, the Triple Timer System is versatile and scalable. It’s designed to integrate seamlessly into any existing setup, offering both flexibility and ease of use. From manufacturers to assembly lines, industries of all types can benefit from this simple yet effective time-tracking solution.
Conclusion
The Triple Timer System is more than just a tool—it’s a strategic asset for improving time management in the factory. By tracking working time, idle time, and problem time in one place, businesses can pinpoint areas for improvement, increase operational efficiency, and reduce downtime. The easy-to-use interface, remote control, master reset functionality, and intuitive ANDON light make it a must-have for any manufacturer looking to stay ahead in a competitive market.
By leveraging this simple yet powerful solution, factory managers can optimize their production processes, create a more productive work environment, and ultimately boost their bottom line. It’s time to take control of your production timeline—one second at a time!
Shop product: DC-256T-UP-ANDON-PROCESS
Watch full operation video: DC-256T-UP-ANDON-PROCESS
DC-Digital Home and Products: DC-Digital
No Comments